Fabrication d’une pièce plastique : Les conseils de conception
Le passage en injection plastique est une étape cruciale dans l’avancée d’un projet. Bien que d’apparence simple, la conception d’une pièce plastique demande de respecter un bon nombre de règles. Voici quelques règles de base à suivre lors de la conception de vos pièces en plastique :
Les épaisseurs
La première, et la plus connue de toutes ces règles est d’avoir une épaisseur constante. Le plastique, étant injecté à chaud, le temps de refroidissement de la pièce doit être homogène afin d’éviter toute déformation. Des épaisseurs non constantes vont donc engendrer des déformations, des retassures, des défauts d’aspect.
En règle générale une pièce injectée présente une épaisseur de parois entre 1,5mm et 4mm. Cela va dépendre bien entendu des matériaux, voici une table que l’on peut trouver facilement sur internet et qui peut servir de premier guide :
Attention, nous entendons souvent parler de soucis liés à de fortes épaisseurs, mais des épaisseurs fines sont également problématiques, cela peut créer des défauts de remplissage (la matière fige avant de remplir la pièce) ou des défauts d’aspect (zones de brillance sur la pièce, zone de recollement)
L’ajout de nervures :
Souvent liées au premier point, les nervures permettent de rigidifier la pièce mais aussi de corriger certaines déformées lors du refroidissement. Ces nervures doivent avoir une épaisseur comprise entre 40% et 60% de l’épaisseur de la paroi sur laquelle elles reposent.
Exemple de nervures : Pièce identique avant/après :
Si les nervures sont trop épaisses ou présentent un rayon (voir point 3), nous allons nous retrouver avec un défaut de retassures et de déformation (voir schéma ci-dessous).
Si à contrario les nervures sont trop fines nous aurons des difficultés de remplissage et donc avec des manques de matières ou du stress dans la pièce.
Prenons le cas type des futs :
Attention aux rayons :
L’ajout de rayons répond à deux problématiques :
- Simplifier la réalisation du moule et donc réduire son coût et ses délais. En effet, certaines arêtes vives internes nécessiteraient de l’électro érosion. L’ajout d’un rayon est souvent lié au rayon de la fraise à utiliser lors de l’usinage du moule.
- Simplifier le passage du plastique lors de l’injection et donc éviter de perturber le flux.
Attention, l’ajout de rayons sur les pièces n’est pas systématique et peut parfois poser problème puisque cela augmente localement les épaisseurs et peut engendrer des déformations.
Voici quelques exemples pour bien comprendre la conception de ceux-ci :
Sans rayon :
Avec rayon 0,5mm :
Les dépouilles
Les dépouilles sont les angles formés entres différentes parois. Celles-ci sont nécessaires à l’éjection de la pièce. Une fois injectée, la pièce refroidit dans le moule, se durcit, mais aussi se rétracte (taux de retrait). La pièce a donc tendance à se fixer sur l’outillage. L’angle de dépouille permet de réduire la surface de contact moule/pièce lors du démoulage, permet donc de faciliter l’éjection et d’éviter trop de contraintes qui pourraient engendrer différents défauts.
Exemple :
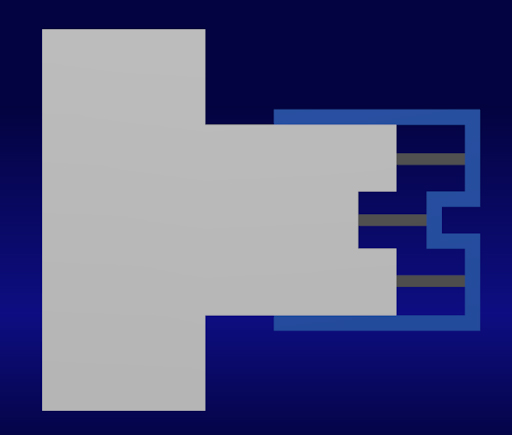
Sans dépouille zone de contact importante
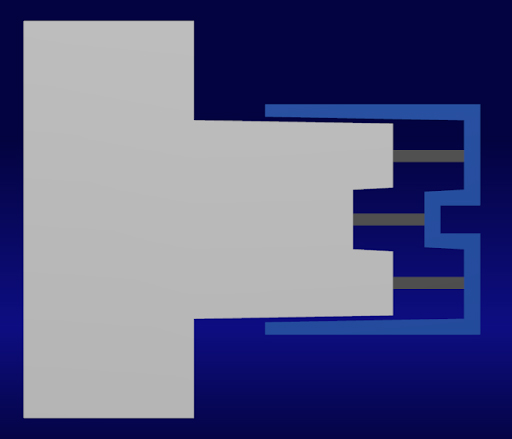
Avec dépouille zone de contact importante
Il faut également faire attention aux zones de fermetures du moule. En effet, dans une zone de fermeture, la dépouille doit être comprise entre 3° et 5° afin d’assurer un bon glissement et la longévité du moule.
Exemple :
Attention cependant, les dépouilles peuvent être nécessaires suivant l’état de surface, un état de surface grainé/texturé va demander un angle de dépouille plus important afin d’éviter les rayures et traces de démoulage extérieur.
Les contre dépouilles
Les contre dépouilles sont des formes non démoulables « naturellement », l’ajout d’un mouvement est obligatoire. Ce mouvement peut être un tiroir (chariot qui vient de l’extérieur du moule, vers l’intérieur), une cale montante, un insert manuel…
Suivant la conception du moule, ces outillages peuvent être automatiques/manuels/pilotés. Ces mouvements permettent de pouvoir éjecter des formes complexes mais augmentent rapidement le coût du moule et de la pièce. Certaines contre dépouilles peuvent être évitées facilement, par exemple avec un clip.
Exemple de contre dépouille :
Analyse simple des deux parties moulantes :
Puis sur la même pièce, une analyse des contre dépouilles (en rouge) :
Nous voyons que pour démouler cette zone, nous allons avoir un besoin d’un mouvement :
Une simple ouverture permet d’éviter un mouvement :
La charnière :
Il est possible de réaliser des charnières en réduisant l’épaisseur locale de plastique et cela couplé avec le bon choix de matière. L’exemple le plus courant est une boîte de dvd. Pour cela il faut, sur le modèle 3D, modéliser sa pièce ouverte, dessiner sa charnière avec une épaisseur généralement comprise entre 0,3mm et 0,5mm et choisir une matière relativement souple telle qu’un PP, un PE ou certains PA.
La conception de la charnière doit suivre quelques règles basiques :
- Rayonner au maximum afin d’éviter tout stress lié au remplissage mais aussi éviter les risques de cisaillement.
- Eviter les zones planes, privilégier un léger « creux » à l’arrière de la charnière afin d’éviter le risque d’entaille, bien connu, à la fermeture.
Voici un résumé des règles de conception :
Le surmoulage
- Le surmoulage peut être de deux grandes familles, le surmoulage Plastique-Plastique (joint sur une pièce rigide, double injection rigide…) ou Plastique-Insert.
Le surmoulage Plastique-Plastique permet la plupart du temps de s’affranchir d’un assemblage (joint, chaussette souple, bumper…). Lors de la conception du surmoulage, il faut faire la distinction entre bi-injection et surmoulage proto via deux moules et souvent injectés sur 2 jours distincts.
En bi-injection, nous pouvons avoir une accroche chimique parfois suffisante entre les deux matériaux, pour cela il faut se rapprocher des fabricants de matières pour choisir les bons grades. Cependant en surmoulage proto, l’adhésion chimique est que très rarement suffisante, il faut alors ajouter des points d’accroches mécaniques (trous traversant…)
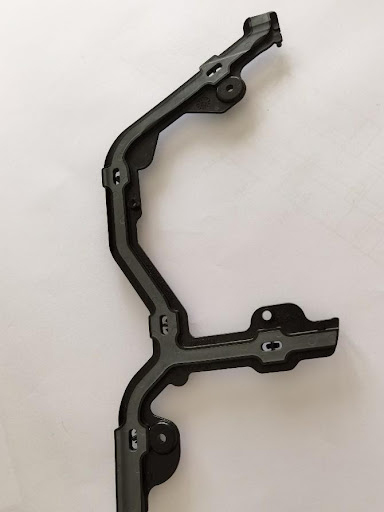
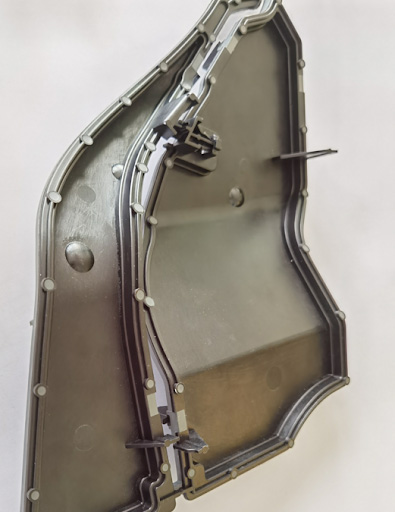
- Le surmoulage d’inserts (souvent d’inserts en laiton pour des futs de vis) permet d’apporter une résistance supérieure au couple de serrage. Cela engendre un coût par pièce légèrement supérieur car un opérateur (en phase proto) ou un robot doit placer les inserts dans le moule avant l’injection (temps de cycle plus long).
Exemple :
Optimiser votre demande de prix
Une fois les principaux conseils appliqués et la conception terminée, il faut également bien décrire le besoin au sous-traitant afin d’éviter de tomber dans la sur-qualité ou au contraire être déçu du résultat. Certains facteurs vont grandement impacter le coût d’un moule d’injection (voir notre article sur la conception des outillages d’injection) :- La durée de vie du projet (en nombre de pièces, exemple : 5000 ou 500 000 pièces) Le nombre de pièces par lot
- L’état de surface attendu (un poli de démoulage suffit ? ou devons-nous polir l’empreinte ? au contraire lui apporter de la texture ?)
- La matière plastique à injecter (un simple PP ? une matière technique telle qu’un PEEK ou un PEI ?)
- Souhaitez-vous récupérer l’outillage ou pouvons-nous utiliser nos carcasses ?